Industrial intelligent equipment operation and maintenance cloud
Reduce the service cost of equipment manufacturers (agents) by 30% and increase the turnover rate of sales by more than 10%
Industrial intelligent equipment operation and maintenance cloud
Reduce the service cost of equipment manufacturers (agents) by 30% and increase the turnover rate of sales by more than 10%
Home / Industrial intelligent equipment operation and maintenance cloud
If you are an equipment manufacturer
Through their own business needs, equipment manufacturers establish their own service processes, master each link of the service process, master customer sales data and equipment data, provide strong data support for after-sales and sales, and provide customers with basic information requirements.
Providing customers with faster, more proactive and less intrusive support will help improve customer service satisfaction and improve the quality of relationships with customers.
If you are a service engineer
The service engineer obtains the repair order status through the computer or mobile phone terminal, views the equipment operation status in real time, views the equipment alarm history, quickly analyzes the equipment exceptions, improves the response speed, quickly queries the equipment related information, and quickly solves the repair order.
Secure remote connection of equipment in all regions can be realized anytime and anywhere to reduce service delay caused by failure to arrive at the site in time. Equipment can be debugged and maintained remotely and directly.
If you are an end user
The end user submits equipment maintenance requirements, equipment information, fault graphic information, etc. through the mobile terminal applet.
At the same time, the terminal user can view the current equipment information, processing parameters and maintenance progress through the mobile terminal applet, and can also monitor the operation rate of the equipment.
Core features
Unified equipment management system
With machine tools and equipment as the core, the company manages machine tool after-sales service, machine tool repair, after-sales service progress, real-time reminder and tracking in a unified system.
Unified BI data central control platform
Realize the statistics and real-time display of machine tool operation data, fault data, machine tool production process data, customer relationship data and other data in the customer's factory.
Real time pull type machine tool sales service
By recording the employee's associated operations on the customer's new machine tools/spare parts/maintenance equipment/maintenance, the customer's portrait is clear, the customer's business situation is predicted and analyzed, and accurate sales strategies are formulated.
Remote operation and maintenance of equipment failure
Through 4G/5G communication gateway, the platform can realize remote connection of machine tool equipment, realize remote equipment diagnosis operation, and reduce maintenance service personnel and costs.
Timely respond to equipment failure operation and maintenance
By configuring the process engine function, the system automatically generates a work record according to the machine tool serial number and fault content, and automatically pushes it to the corresponding after-sales service personnel after distribution. The system does not respond to the real-time reminder in case of overtime.
Global multi platform service support
It not only supports domestic mainstream Alibaba Cloud, Huawei Cloud and other PaaS platforms, but also supports international popular cloud service provider platforms, such as Azure, AWS, GCP, etc.
Full lifecycle management of equipment information
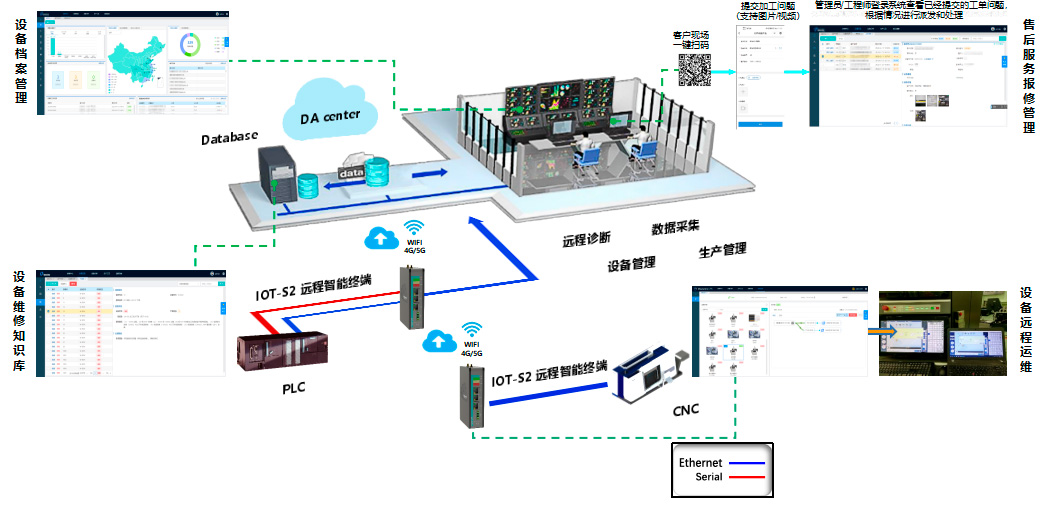
If you are an equipment manufacturer
Through their own business needs, equipment manufacturers establish their own service processes, master each link of the service process, master customer sales data and equipment data, provide strong data support for after-sales and sales, and provide customers with basic information requirements.
Providing customers with faster, more proactive and less intrusive support will help improve customer service satisfaction and improve the quality of relationships with customers.
If you are a service engineer
The service engineer obtains the repair order status through the computer or mobile phone terminal, views the equipment operation status in real time, views the equipment alarm history, quickly analyzes the equipment exceptions, improves the response speed, quickly queries the equipment related information, and quickly solves the repair order.
Secure remote connection of equipment in all regions can be realized anytime and anywhere to reduce service delay caused by failure to arrive at the site in time. Equipment can be debugged and maintained remotely and directly.
If you are an end user
The end user submits equipment maintenance requirements, equipment information, fault graphic information, etc. through the mobile terminal applet.
At the same time, the terminal user can view the current equipment information, processing parameters and maintenance progress through the mobile terminal applet, and can also monitor the operation rate of the equipment.
Core features
Unified equipment management system
With machine tools and equipment as the core, the company manages machine tool after-sales service, machine tool repair, after-sales service progress, real-time reminder and tracking in a unified system.
Unified BI data central control platform
Realize the statistics and real-time display of machine tool operation data, fault data, machine tool production process data, customer relationship data and other data in the customer's factory.
Real time pull type machine tool sales service
By recording the employee's associated operations on the customer's new machine tools/spare parts/maintenance equipment/maintenance, the customer's portrait is clear, the customer's business situation is predicted and analyzed, and accurate sales strategies are formulated.
Remote operation and maintenance of equipment failure
Through 4G/5G communication gateway, the platform can realize remote connection of machine tool equipment, realize remote equipment diagnosis operation, and reduce maintenance service personnel and costs.
Timely respond to equipment failure operation and maintenance
By configuring the process engine function, the system automatically generates a work record according to the machine tool serial number and fault content, and automatically pushes it to the corresponding after-sales service personnel after distribution. The system does not respond to the real-time reminder in case of overtime.
Global multi platform service support
It not only supports domestic mainstream Alibaba Cloud, Huawei Cloud and other PaaS platforms, but also supports international popular cloud service provider platforms, such as Azure, AWS, GCP, etc.
Full lifecycle management of equipment information
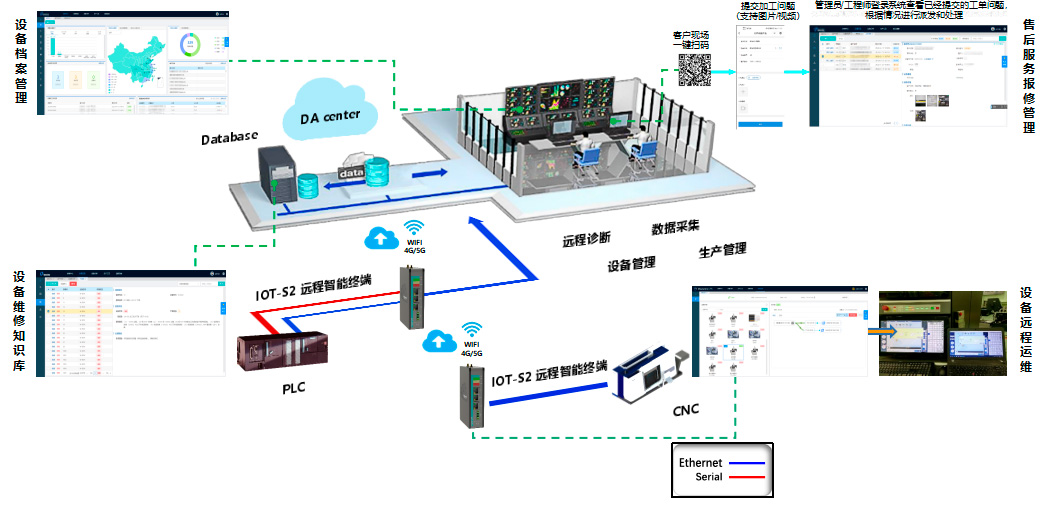
COUNT FOR MORE
Please leave your contact information and our customer manager will contact you as soon as possible
COUNT FOR MORE
Please leave your contact information and our customer manager will contact you as soon as possible
Contact us
Hotline
400-828-3830
E-mail
Sales@wimisoft.com
-
Official account
Copyright © 2021 MasterLink All Rights Reserved.
苏ICP备19005118号-1
Product trial